SkullandBonesSkateboards.com Forum Index » MANUFACTURERS FORUM » Mold Material |
Page 1 of 2 Goto page 1, 2 Next |
|
Author |
Message |
Everide |
Posted: Sun Jul 16, 2006 1:35 pm |
|
|
Joined: 16 Apr 2006
Posts: 81
Location: MidWest
|
Just wanted to know if anybody has any suggestions on what to use to make the molds for my press.
I'm thinking either concrete or a resin of some sort. Any other ideas?
Here is a drawing of what the press will look like:
http://img45.imageshack.us/img45/1414/ddcr1.jpg |
|
|
Back to top |
|
|
CH3NO2JAY |
Posted: Mon Jul 17, 2006 4:15 pm |
|
|
Joined: 13 Jan 2002
Posts: 7303
Location: Chicago
|
Link doesn't work for me.
Probably the cheapest way to go is Cement.
I still wonder what a big Urethane or Alloy mold would cost via a CNC machine instead of concrete. |
|
|
Back to top |
|
Lincolnz |
Posted: Mon Jul 17, 2006 4:45 pm |
|
|
ORDER OF THE SKULL
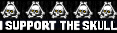
Joined: 05 Jun 2005
Posts: 11215
|
CH3NO2JAY wrote: Link doesn't work for me.
Probably the cheapest way to go is Cement.
I still wonder what a big Urethane or Alloy mold would cost via a CNC machine instead of concrete.
Getting one milled out of alloy would be pricey.
I wonder how delerine(sp) would work or if it would be too soft.
Or making one out of a solid block of hardwood.
We my brother makes his mold for the yahts he builds he makes them out of fiberglass and does a vaccum method. I don't imagine it would hold up to a hydro press. |
_________________ The reason I'm fat is, every single time I fuck your mom, she makes me a sandwich. |
|
Back to top |
|
|
Everide |
Posted: Mon Jul 17, 2006 5:24 pm |
|
|
Joined: 16 Apr 2006
Posts: 81
Location: MidWest
|
I know cement is the cheapest way. You can reinforce it with rebar and that fiber they put in. I talked to a guy about it and he suggested 60 carbon rebar every 4 inches, several layers, and adding the fiber. I forgot what the bag count was though.
I also looked into melting aluminum. Seems like it would work nicely if you are ambitous:
http://www.backyardmetalcasting.com/
It would be a little more work, but would last really long. I figured about 4-7 gallons of molten aluminum for one half of a mold. You'd just need to drink a lot of beer
I'll probably do it with cement until I can upgrade. |
|
|
Back to top |
|
pennswood |
Posted: Mon Jul 17, 2006 5:26 pm |
|
|
Joined: 14 Sep 2003
Posts: 213
|
we have used everything.
cement is the cheaper way to go.
but it takes up to 30 days to have enough cure.
also it is under much pressure, and has a tendency to explode.
there are some additives you can put in to help.
next is wood,
a solid wood or laminated block,
slices of the concave shape are vertically laminated,
then sanded into shape.
high level of craftsmanship and tools.
then we have a poured urethane product.
the cost if you dont fuck it up is about $ 300 per mold set.
this product is a 2 part liquid
when mixed together then poured into a mold form,
it hardens to amazing levels in about 2 hours.
this will require a mold form for the pour,
and a high level of skill to build the form.
then we move into cnc molds,
requires a 3-d cnc mill,
with a very complex cutting program,
each side of our mold, top and bottom,
are cut to perfect tolerances,
from a huge piece of aluminum that cost about $ 2000,
it took 20 hours of cnc time to cut each half.
then i paid to have a board laser scanned,
from one of our previous handmade molds.
then we threw some geometry on it with a 3-d CAD.
i had to pay the cad guys another $2000 for the programming.
we paid to have 5 mold sets done, and it was not cheap.
so what i have come to now is we just duplicate the exsisting
cnc cut molds with the urethane method.
i should have not cut all our initial 5 molds from aluminum.
just made 1 set for perfect mold forms. |
|
|
Back to top |
|
Dan |
Posted: Tue Jul 18, 2006 7:07 am |
|
|
Joined: 11 May 2005
Posts: 45
Location: USA
|
Overflowing with metal(aluminium or else ) is not recomended couse metal when cools has trends,tendence to shrink near 1/3 inches,any polishing not gave result. |
|
|
Back to top |
|
|
Lincolnz |
Posted: Tue Jul 18, 2006 8:31 pm |
|
|
ORDER OF THE SKULL
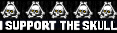
Joined: 05 Jun 2005
Posts: 11215
|
pennswood wrote:
then we move into cnc molds,
requires a 3-d cnc mill,
with a very complex cutting program,
each side of our mold, top and bottom,
are cut to perfect tolerances,
from a huge piece of aluminum that cost about $ 2000,
it took 20 hours of cnc time to cut each half.
then i paid to have a board laser scanned,
from one of our previous handmade molds.
then we threw some geometry on it with a 3-d CAD.
i had to pay the cad guys another $2000 for the programming.
we paid to have 5 mold sets done, and it was not cheap.
so what i have come to now is we just duplicate the exsisting
cnc cut molds with the urethane method.
Yeah I use to work in a machine shop making molds. The shit ain't cheap at all. |
_________________ The reason I'm fat is, every single time I fuck your mom, she makes me a sandwich. |
|
Back to top |
|
devotid |
Posted: Thu Aug 10, 2006 11:03 pm |
|
|
Joined: 20 Apr 2006
Posts: 26
Location: saginaw, MI
|
Ive made three cement molds with rebar in them and use them for pretty high production making wakeskates. works great. the two part epoxy system is exspensive and i made a mess trying it with some stuff from a guy at QCM technologies. google it and ask for roy. hes as cool as a fan.
just didnt work for what im doing.
my 2 cents |
|
|
Back to top |
|
Everide |
Posted: Sat Aug 12, 2006 8:47 pm |
|
|
Joined: 16 Apr 2006
Posts: 81
Location: MidWest
|
Yeah, I chose the cement route. I made it a three cavity press. Popped the first board out yesterday
The cement seemed to hold out pretty well. I made each mold 28" thick (top and bottom combined) put two vertical and two cross layers of rebar and added fibermesh. seemed to work out ok.
Only problem I had was when my molds were open my cylinder didn't fit. I'll have to revamp the press a bit.
If I get a chance I'll post a pic or two. |
|
|
Back to top |
|
|
fishbowlproject |
Posted: Sun Aug 20, 2006 9:24 pm |
|
|
Joined: 10 Aug 2006
Posts: 62
|
Everide, Did you have more sucess troweling the concave or making a pre-form from another material? Thanks |
|
|
Back to top |
|
|