SkullandBonesSkateboards.com Forum Index » SCREEN PRINTING » home made printers and registration |
Page 1 of 1 |
|
Author |
Message |
soze' |
Posted: Tue Jun 15, 2004 12:53 am |
|
|
Joined: 14 Jun 2004
Posts: 2
|
hey, ive had a good look through almost every post on this forum, and its been really helpful but theres a few things that have gone over my head.
1.Ok, say you have a 4 colour, 1 station screen machine setup. Youve done your first colour pass and you rotate the screens to the next colour, but the tee has to be dry before you can do the 2nd pass. Does the shirt get removed, dried, then put back on the jig and re-alligned with the 2nd screen? (im guessing no because this would be slow as shit, and hard to re-allign.) Is the first pass dried while the tee shirt stays clipped into the jig? wouldnt all the heat dry the ink on the screen that is raised up above the t-shirt, and clog it up?? I know this is probably simple.. im sure ive just missed something.
2. Do proper machines have micro adjustments on the arms of the machine to perfectly register the screen to the tee? Or is it the base board that you move to allign with the screen? OR are you supposed to burn all the images on exactly the same spot on all 4 screens initially?Then just lock em all into your printer and go for it
3. Do you need a proper darkroom with special lights to apply the light sensative emulsion , or could a dim room do the trick
4.Any tips on what kind of wood to use for the screens? anything? pine? hardwood?
5.Ive read a few times that people keep the screens a few millimeters off the t-shirt to help ink flow. Other sites with screening instructions make no mention of leaving a gap between the screen and the shirt. Is it necessary, and if so how do you keep it a few MM off? Do you tape some cardboard around the bottom edges of the frame or is that adjustment supposed to be built into the screen printing machine? (wouldnt this put extra pressure on the actuall screen, since the squeegee isnt pushing on the shirt, only the screen material?)
6. Proper brand name shirts, made large scale, are surely not screen printed these days... are they made with 'pad printing' that ive read about, or an advanced and automatic screen printer, or what?
7. Ive scoured the net for a long while for tips, directions etc (this forum has been one of the best finds)... wondering if others have done the same and if there are any good sites out there? IM particularly interested in peoples home built jigs like the ones some people posted on here.
heres are some sites ive found with basic instructions for screening..
http://waapa.ecu.edu.au/disc/sova/pri...l/screenbody.html
http://www.nehoc.com.au/training/index.htm
http://www.chsscout.net/rescenter/docs/printing/silk.htm
Any help with any of my questions will be great. Cheers....
|
|
|
Back to top |
|
|
altomic |
Posted: Tue Jun 15, 2004 1:55 am |
|
|
ORDER OF THE SKULL
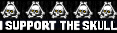
Joined: 30 Sep 2003
Posts: 2098
Location: here and there
|
SORRY I DONT HAVE ANY ANSWERS TO YOUR QUESTIONS BUT I JUST WANTED TO SAY THAT THEY ARE THE SAME QUESTIONS I HAD.
THOUGH I HAVE ANOTHER QUESTION. WHEN SCREENING MULTI COLORS, BETWEEN COLORS CAN YOU USE A HAIRDRYER TO DRY THE INK OR SHOULD IT DRY NATURALY? |
|
|
Back to top |
|
PASS |
Posted: Tue Jun 15, 2004 6:44 am |
|
|
Joined: 19 Nov 2002
Posts: 217
Location: Oregon
|
Well... I'll attempt some of your questions, mind you this is only based on my personal experience (15+ yrs) printing as a side biz and at home.
1. if using plastisol ink with proper color seperation you can print "wet on wet".. from my experience it works better "wet on wet" when you don't have to color trap you design/seperations... otherwise it tends to "pull" some of you first ink off the T. My adivse would be to make you homemade printer a 4-color 4-station (as i once did), that way you could "flash" in between colors alowing wet on wet or color trapping.
2. Yes, professional printers have micro registration and/or knobs to adjust height, left and right..forwards and backwards, but if your doing a home made printer you wont have that luxury.. you'll have to align you design as close as possible for the "burn", then adjust the whole frame within you clamp/hinges.
3. low light will work.. i use to work out of a laundry room with the door cracked open..or plug in a lamp using a yellow bug light..
4. wood or alluminum is the norm... there are self tightening frames as well..(newman frames).. but they don't work well on homemade printers... at you local screen printing supply store they should offer wood and/or alluminum frames..even pre-stretched in different mesh counts.
5. i usually try to set the design barely off the t-shirt.. 1/8 or so.. if it touches.. usually no big deal as long as you've flashed in between colors.. otherwise you pull up some of the ink as mentioned before.
6. Hmm... my guess the big operations are using the same method, but utilizing an automated printer.. meaning once everything is registered.. a dude just loads the shirts at one station, while pneumatic arms do all the work..hehe
7. Visit you local screen supply store.. many carry basic "how to" books... that's where I modified the 4 color 2 station printer into a 4 + 4... I mean, who wants to bounce around..i like standing in one place and swing the T palets to me... you might also check at local screen shop about "renting space".. there are 2 shops here in honolulu that do that (avg is $20/hr)
I should write a "how to homemade" book..lol
Hope this helps.. wish I had a pic of the printer I made (sold it).. don't think I do, the design is all in the head.. I used it for 7 years before selling it... so they'll last and give you surprisingly good registration.
BDK
|
_________________ skate like there's no tomorrow |
|
Back to top |
|
|
soze' |
Posted: Wed Jun 16, 2004 3:49 am |
|
|
Joined: 14 Jun 2004
Posts: 2
|
thanks heaps mate,
when you say "flash it" between passes, can that be a poxy job with a heatgun, or are you talking about using a proper globe or something that cooks it at the correct temperature?
Also, what order do you work on the shirts using a 4 colour 4 station machine? im just trying to get the process straight in my head..
eg. Do you work on one shirt at a time, flashing between each pass, then move onto the next shirt. OR do you do the first pass on all 4 shirts, drying them while you work on another shirt, then do the 2nd pass on all 4 shirts etc etc..?
|
|
|
Back to top |
|
PASS |
Posted: Wed Jun 16, 2004 1:41 pm |
|
|
Joined: 19 Nov 2002
Posts: 217
Location: Oregon
|
The term "flash" actually means skin curing the ink on the shirt... this is done by a panel (Infrared Heat Panel) that can be moved over the t-shirt pallet at a different station... in other words while your standing at one of your 4 stations printing, the flash unit would be skin curing the plastisol ink on the first shirt at the following station. Those flash units are the same thing that's in a conveyor dryer, except there would be 1-3 panels, depending upon the size of the dryer... btw flash units are only required for some types of multi color printing..and when you have to need to print a white base first on a shirt (blk or ver dark), then print the colors on top..in order to do that you have to "skin" cure the wht ink first..via the flash unit.
Plastisol ink are the mainstream norm for t-shirt printing..the ink never drys (cures) unless it hits 375 degree or so.. the flash unit will skin cure the ink though in a matter of seconds (5-15 sec) when placed about an inch or so above the t-shirt pallet.. ((warning)) you can "cook" a t-shirt if you forget you left it under the flash unit...lol the plastisol ink is the best..wide variety of colors, puff inks, elastic inks..and additives avail for printing on nylon, etc..etc.. I use to just store my frames wet with the ink still in it..then just plop down more ink the next time printing that design.. no probs..it never drys.
9.9 times out of 10, the color print pattern is light to dark...
hope this help..
BDK
http://secure.usscreen.com/catalog/index.cgi?pid=2
http://www.fuellesspower.com/solar_cell2.htm
http://secure.usscreen.com/catalog/index.cgi?pid=3
|
_________________ skate like there's no tomorrow |
|
Back to top |
|
altomic |
Posted: Fri Jun 18, 2004 8:30 pm |
|
|
ORDER OF THE SKULL
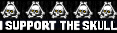
Joined: 30 Sep 2003
Posts: 2098
Location: here and there
|
I guess you could make a identical racks to hold the tshirts with the same peg holes to hold the screens. yeah?
I saw a show on TV about screening t`s in japan. they had this wooden rack that would hold ten tshirts in row. each rack had identical markings so that the printer would just walk along the rack and bang bang bang, ten tshirts one colour. by the time he got to the end an cleaned that screen it would be time to do the colour.
that looked like a sweet and "easy" process. |
|
|
Back to top |
|
|
|