SkullandBonesSkateboards.com Forum Index » SCREEN PRINTING » White on black shirts...help! |
Page 1 of 2 Goto page 1, 2 Next |
|
Author |
Message |
racerxmccoy |
Posted: Mon Feb 19, 2007 9:02 am |
|
|
Joined: 19 Feb 2007
Posts: 3
|
I own a small vinyl graphics company that does mostly stickers and car graphics. I recently decided to try screen printing. So far I've done okay with printing on white shirts, but now I have someone that wants white ink on dark colors shirts and I'm pulling my butt hair out trying to get it right . I'm using Triangle Phoenix white ink, through new 110 mesh screens. First off it looks like all the color isn't going through the mesh in places, even though I'm pressing the hell out of my squeegie, second if I flash and then reprint the graphic comes out all bumpie and uglie looking. Is my ink too thick?
Any help is much appreciated. |
|
|
Back to top |
|
|
badgoldfish |
Posted: Mon Feb 19, 2007 12:01 pm |
|
|
Joined: 20 Sep 2005
Posts: 406
Location: kalamazoo-michigan
|
---WHITE ON BLACK IS THE BITCH OF THE INDUSTRY--
--problem #1, you should'nt have to press the hell out of your squeegie, are you using a stiff one or a flexi one - i use stiff
---problem #2 off contact is very important - not too much or too little
---problem #3, sounds as though your screens may not be exposed properly, i.e. ink not going through everywhere (are you doing a flood print then the actual print?) i do a flood pull - then print - then sometimes a "dry" pull
---problem #4, unless you want a real thick print 110 mesh is too loose - i run white ink through 180 to 230 (depending on detail) all the time and get nice even flat prints -( i also use retensionable screens which are vastly superior to untensionable frames)
-- what sort of flash ?? is it just a oven element type(these suck - uneven heating will give you all sorts of trouble - get a quartz flash
-- you should only need 5 to 7 seconds of flash, too much is bad as is too little
-- i use union bright cotton white for cotton and their diamond white for 50/50, but just got some creamy white from QCM inks which i may like more but i'm still testing
---check the forums on screenprinters.net - IT WILL HELP THE MOST OF ALL
-------but the easiest is just to let someone else do it.
hope there's some help in there for you --ryan |
_________________ www.goldfishprints.net |
|
Back to top |
|
Stranglehold77 |
Posted: Mon Feb 19, 2007 10:35 pm |
|
|
ORDER OF THE SKULL
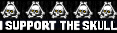
Joined: 10 Apr 2002
Posts: 5437
Location: Victoria BC CANADA
|
badgoldfish wrote: ---
---problem #4, unless you want a real thick print 110 mesh is too loose - i run white ink through 180 to 230 (depending on detail) all the time and get nice even flat prints
I NEVER hit white on anything higher than 155 (unless it's something with crazy small halftones). You'll hurt yourself pushing white through that tiny mesh!
I aggree that screenprinters.net is a good place for answers.
Ty |
_________________ STIFF HOMBRE!!!!! |
|
Back to top |
|
|
Earwick66 |
Posted: Tue Feb 20, 2007 12:17 am |
|
|
Joined: 27 Oct 2005
Posts: 3565
Location: Grand Saline,TX
|
on most all designs(unless 1/2 tones are in the art like Stranglehold77 said)my favorite mesh for white ink on dark shirts is a 156..for me its the "perfect" all-around mesh count for white on dark shirts.
even with 1/2 toned art, i try to gradually bump it up to like a 175/180 before having to go drastic(230/305)
the ink you are using(Triangle Phoenix white) is generally "ready to go" right from the bucket, but if youre experiencing these problems you may want to add a little "curable reducer" or some "soft hand" additive to make the ink flow better thru your screen and make your prints smoother.
i have experienced certain brands of shirts that give me that "fuzzy" texture more so than other brands and sometimes its a matter of a little experimentation till you get a smooth print.
depending on how big the logo is(how much ink your putting down)you may also want to allow a few seconds for the shirt to cool off after flashing before you hit it again(i use a simple piece of cardboard to fan it off or you could set up a small fan)
Good Luck and check out a few other forums for more help but feel free to ask more questions about specific problems on here  |
|
|
Back to top |
|
Fool's Gold |
Posted: Tue Feb 20, 2007 8:42 am |
|
|
Joined: 10 Mar 2005
Posts: 284
Location: Ontario Canada
|
Stranglehold77 wrote: badgoldfish wrote: ---
---problem #4, unless you want a real thick print 110 mesh is too loose - i run white ink through 180 to 230 (depending on detail) all the time and get nice even flat prints
I NEVER hit white on anything higher than 155 (unless it's something with crazy small halftones). You'll hurt yourself pushing white through that tiny mesh!
I aggree that screenprinters.net is a good place for answers.
Ty
280-305 baby!
White ink so so over pigmented (like most other inks) that you can add a fair amount of soft hand and reducer to make it flow. There should be no problem getting a cotton white (not 50.50 or poly whites) to got though a 230 mesh screen, if you can't do it, add reducer. There is no different in opacity betweeen hitting a 157 twice, or a 230 twice.
Push stroke, way better for the arms and way better pressure/stroke. Use your back to print, not your little wrist muscles. The weight of your body will make white printing so much easier.
Make sure your platen is flat and clean too. The bumpier, dirtier and uneven it is the lower mesh you need to use to deal with those dips and valleys.
Warm your ink and stir your ink for about 15 minutes under a drill press mixer. |
_________________ IRONCLAD GRAPHICS: Custom screen printed posters, apparel and stickers. |
|
Back to top |
|
badgoldfish |
Posted: Tue Feb 20, 2007 9:02 am |
|
|
Joined: 20 Sep 2005
Posts: 406
Location: kalamazoo-michigan
|
it works different for everybody. i "warm" up the ink for 10 to 15 min. with a paddle bit to make it flow. |
_________________ www.goldfishprints.net |
|
Back to top |
|
|
badgoldfish |
Posted: Tue Feb 20, 2007 9:06 am |
|
|
Joined: 20 Sep 2005
Posts: 406
Location: kalamazoo-michigan
|
|
Back to top |
|
Fool's Gold |
Posted: Tue Feb 20, 2007 11:00 am |
|
|
Joined: 10 Mar 2005
Posts: 284
Location: Ontario Canada
|
one problem using a fine mesh causes with white ink is in large open areas. Unless you have really tight screens, it's helpful to lower the meshcount so the squeegee doesn't bind up on the large areas of open mesh.
another interestin option is to do some tests with various halftone counts (LPI) to see at which % dot you mash out all the detail. Meaning: the 0-20% dots will probably fill in to form a solid colour, not a gradient. It's called dot gain (in case you didn't know that) SO, say you had a square to print, and knew that when you get to the a certain % halftone dot you don't see halftones but a solid tone. Then in theory, because of the dot gain, you could print that square with a 20% halftone fill (80% open mesh, 20% dots) in theory you should be getting a solid coating of white. Double hit that and you have a solid tone, but the amount of ink left on the shirt is less. same opacity, thinnner ink film, softer shirt, faster flash, less ink used. all good things. |
_________________ IRONCLAD GRAPHICS: Custom screen printed posters, apparel and stickers. |
|
Back to top |
|
racerxmccoy |
Posted: Sun Feb 25, 2007 8:07 am |
|
|
Joined: 19 Feb 2007
Posts: 3
|
you guys are the best! I tried or double checked everything that you guys rsponded with and guess what? it was a little bit of everything. The major factor was that my off contact was way off and not at all level. the second major issue was the adhesive that I was using to secure my shirts to the platens was a web spray and it wasn't holding my shirt down. I took a while just to think everything through, but now I'm smooth sailing! |
|
|
Back to top |
|
|
sheltered |
Posted: Sun Feb 25, 2007 1:14 pm |
|
|
Joined: 16 Sep 2005
Posts: 86
|
Yeah....there is flashable textile adhesive and regular. I've made that mistake before! The off contact thing is huge. I used to print a lot of flat stock and off contact is paramount. T-shirts can be so forgiving sometimes we forget the basics. |
|
|
Back to top |
|
|