SkullandBonesSkateboards.com Forum Index » SCREEN PRINTING » Is it compadable? |
Page 1 of 1 |
|
Author |
Message |
Damote Skate |
Posted: Sat Mar 12, 2005 3:04 am |
|
|
Joined: 30 Jun 2004
Posts: 10
Location: Reno
|
i am going to get most of my equipment through dick blick and was planning on using union ultrasoft plastisol plus inks with ulano qtx emultion and 232 count white mesh. Does this setup sound right or should i change up some of the stuff?
I plan on printing on all color fabrics
Thanks, Shane |
|
|
Back to top |
|
|
thevagrant |
Posted: Sat Mar 12, 2005 1:04 pm |
|
|
Joined: 18 Mar 2003
Posts: 19
|
a 232 count mesh is way too high for printing plastisol inks. your best bet for all color shirts is to use 110-180 mesh. with a 232 you'll be printing let's say white ink on black shirts with like 4-5 hits and it will still look crappy. |
|
|
Back to top |
|
skinny |
Posted: Sat Mar 12, 2005 1:28 pm |
|
|
Joined: 12 Sep 2004
Posts: 2706
|
Yeah the emolusion is great and plastisol is the best for shirts, but I would go get a lower mesh count, and I would get monofiliment. 156 is a good place to start. 230 and higher is for enamel paint. |
|
|
Back to top |
|
|
Stranglehold77 |
Posted: Sat Mar 12, 2005 1:29 pm |
|
|
ORDER OF THE SKULL
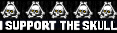
Joined: 10 Apr 2002
Posts: 5437
Location: Victoria BC CANADA
|
I typically use 155-175 for standard printing and higher mesh for process inks. |
_________________ STIFF HOMBRE!!!!! |
|
Back to top |
|
newrepublicsteve |
Posted: Sat Mar 12, 2005 7:19 pm |
|
|
Joined: 13 Nov 2004
Posts: 674
Location: Birmingham
|
I use 110 and 155 for most prints
230 and even 305 for highend half tone work
if you thin your plastiasol you can get nice soft hand prints in 2 passes on high mesh, but for starting out go 110 |
|
|
Back to top |
|
Fool's Gold |
Posted: Sun Mar 13, 2005 10:27 am |
|
|
Joined: 10 Mar 2005
Posts: 284
Location: Ontario Canada
|
157-200 mesh is what we use at our shop for most printing. I would suggest not getting the ultrasoft ink, but get the Union MaxOpake series, as well as a tub of clear base. With the Max you can direct print on black shirts with no underbase, and with the clear base you can thin the ink down to print on light shirts. |
_________________ IRONCLAD GRAPHICS: Custom screen printed posters, apparel and stickers. |
|
Back to top |
|
|
Damote Skate |
Posted: Mon Mar 14, 2005 12:25 am |
|
|
Joined: 30 Jun 2004
Posts: 10
Location: Reno
|
thanks for the help everyone
fool's gold when you say the clear base are you just talking about the maxopake's reducer/detack and if I did go that route i didn't see a black ink of the maxopake do you just use the ultrasoft then? |
|
|
Back to top |
|
Fool's Gold |
Posted: Thu Mar 24, 2005 1:56 pm |
|
|
Joined: 10 Mar 2005
Posts: 284
Location: Ontario Canada
|
Damote Skate, by clear base i am referring to plastisol with NO pigment in it. The pigment content is one factor that determins how thick the ink is. Stir some black and then stir some white, white is thicker because it needs the most pigment to cover up dark colour shirts. If you are using the Union MaxOpake inks they have a lot of pigment because they are designed to be printed directly onto black shirts. Since they have so much pigment you can add sometimes up to 300% clear base to any maxopaque colour to and there will still be enough pigment to cover the white shirts, it also allows you to extend the life of your ink. So what clear plastisol base does is make your final print soft, not thick and hard like if you printed straight out of the can. Always stir your ink for at least3-5 minutes with a power drill and allen key, this will thin the ink down.
Curable reducer/Detackifier (PLUS-9000 I believe is the prod #) on the other hand serves another purpose. This
A) allows you to thin the ink so it will pass through higher mesh counts. We print white on black with 200 mesh, only use 110 when we print sweats, or maxopake on black. Being able to print on 200 mesh all the time is great because you use less emulsion, shorter burn times, thinner print, more detail, smoother print.
B) removes the 'tack' that causes ink to build up on the back of screens during multi colour printing. You should be able to print an underbase then as many colours as possible, wet on wet, before you need to flash again. If you try printing wet on wet and the screen sticks to the black of the next screen, or pulls up the colour before, then add curable reducer/detack, it will reduce this.
We add a combination of both to all our inks before we print, sure it's an additional half an hour added to setup, but you cut production into a quater if you need to flash after each colour. Remember that you can't add too much of either of these things before the opacity of the ink deteriorates. |
_________________ IRONCLAD GRAPHICS: Custom screen printed posters, apparel and stickers. |
|
Back to top |
|
|